Molding
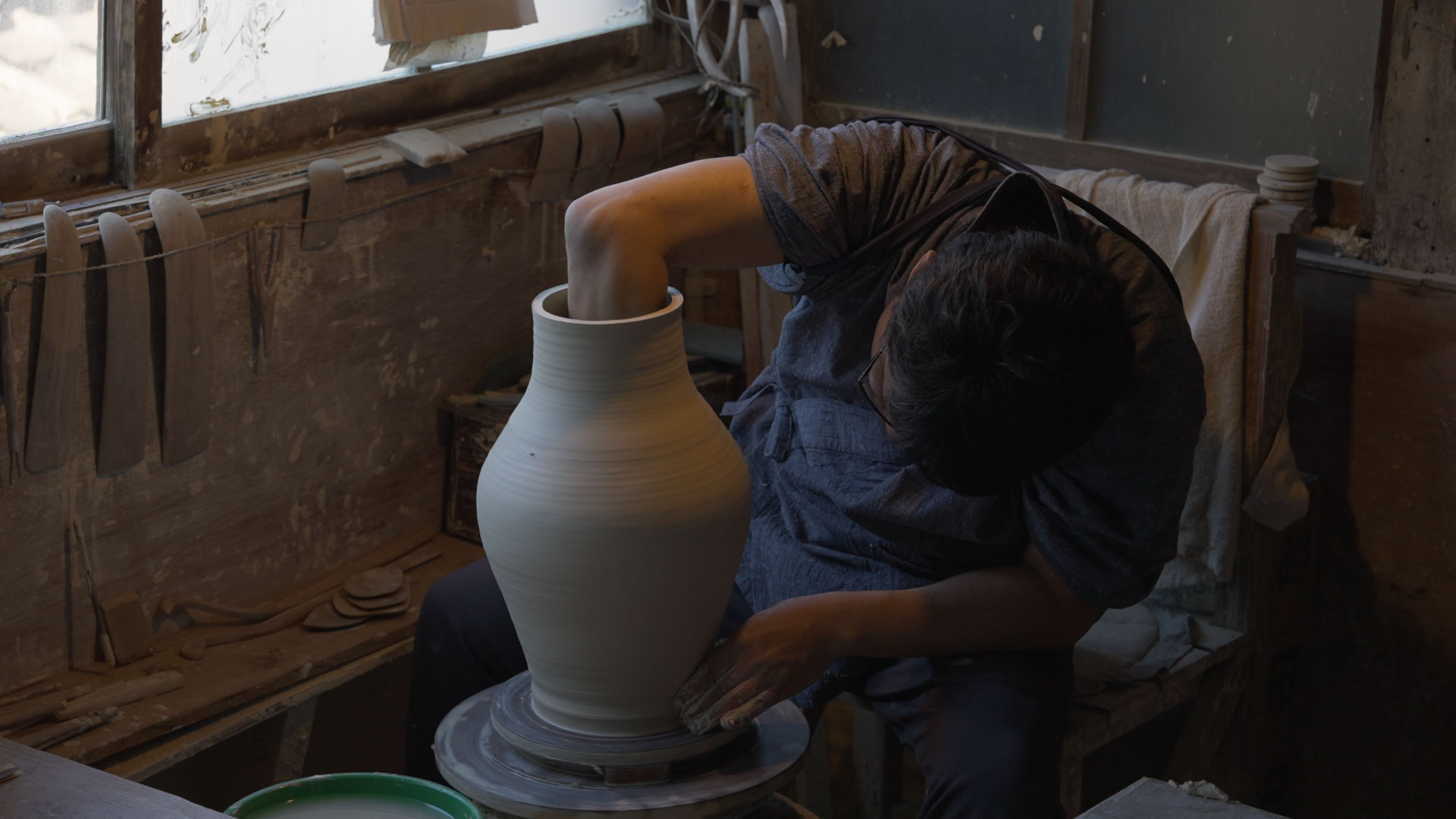
01Case
- Prototype
- A prototype of the product you have in mind is created. In today's ceramic industry, it is possible to express oneself in ways that go beyond the imagination of existing ceramic designs, from hand-quality molds created by a sculptor to computer-controlled NC cutting machines using 3D-CG data and other cutting-edge equipment.
- Sample type (original type: discarded type)
- Based on the prototype, a test prototype called a sample mold (discarded mold) is made, and the actual shape of the fabric based on the prototype is examined. At this point, if there are any modifications, they are reflected in the mold and verification is repeated.
- Case type
- Using the final sample mold that has been revised and verified, a case mold is made. This case mold is then used to make the actual mold for mass production of the pottery dough (use mold).
- Use type (mass production type)
- The plaster mold used to make the raw material for pottery is called the use mold. When a mold is used for a long time, wear and deterioration can affect the raw material, so a new mold is made using the case mold as the base.
02Hand Wheel
This is a ceramic forming machine that uses centrifugal force to grind potter's clay into a beautifully shaped rotator. There are various types, but in recent years, the motorized potter's wheel has become the mainstream.
03Mold
This is a forming technique in which a soft, raw, dry base is covered with a mold and beaten to deform it, copying the shape of the mold and the carved patterns. It can be used to create non-circular and complex shapes such as flowers and polygons, which cannot be formed using a potter's wheel alone.
04Wheel
In the molding method using a mechanical wheel, a plaster mold is placed on a stand made of plaster called a dowel, and while rotating, a spatula attached to the handle is used to press and scrape the dough into shape. It is also called a water iron because it is powered by electricity and uses water for shaping. Due to the characteristics of the machine wheel, it is mainly used for forming rotating objects such as bowls and cups, and can be used for a wide variety of products in small lots.
05Roller Machine
In this method, ceramic clay is put into a special plaster mold shaped like a vessel, and pressed and stretched by a metal head roller rotating at high speed to form the dough. Like the machine wheel, this method is suitable for forming rotating objects, but it uses heat instead of water for forming, and is characterized by its ability to produce stronger and more precise fabrics. This method is also very productive and is suitable for mass production.
06Drain Casting
This is a molding technique that uses the water-absorbing properties of plaster. After the required thickness is achieved, excess mud is drained from the mold to form the dough. It is mainly suitable for mass production of hollow products such as teapots and vases.
07Pressure Casting
In this method, a pair of plaster molds, one convex and one concave, are stacked on top of each other, and pressure is applied to pour mud into the molds to form the dough. The plaster is removed from the molds after it has hardened to an appropriate thickness due to the water absorbency of the plaster. This method is mainly suitable for mass production of special vessel shapes such as deformed or embossed ones.
083D Modeling
Using state-of-the-art equipment such as NC cutting machines that use 3D-CG data, etc., plaster is automatically processed by computer control to create prototypes and casting molds. Regular and precise edges and shapes that are difficult to achieve with hand quality can be expressed.